Doug Jacobson’s leadership in cyber security research and education began before high-speed internet, smartphones and Google. It even predates the term “cyber security” itself. Jacobson, Stanley Chair in Interdisciplinary Engineering, University Professor of electrical and computer engineering, and director of the Center for Cybersecurity Innovation and Outreach, was one of the few who saw “information … Continue reading Writing the Script
Category: Research Highlights
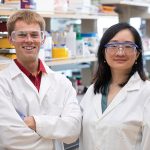
Powerhouse of the cell, key to new treatments: Mitochondrial DNA manipulation offers insights into related diseases
If you remember just one thing from high-school biology, it’s that the mitochondria are the powerhouses of the cell. But could mitochondria also hold the key to gene therapy and new tailored drug development for diseases and disorders? Zengyi Shao, Vernon Guse Faculty Fellow and associate professor of chemical and biological engineering, and her team … Continue reading Powerhouse of the cell, key to new treatments: Mitochondrial DNA manipulation offers insights into related diseases
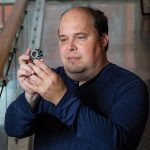
More than the sum of its parts
Additive manufacturing (AM) holds the promise of transforming nearly every way that materials and components are conceived, designed, produced and used in service. The possibilities and expected innovations are numerous, and their realization requires a truly multidisciplinary cadre of researchers. Here at Iowa State, researchers are at the forefront of additive manufacturing, conducting leading research … Continue reading More than the sum of its parts
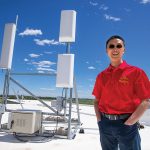
Wireless Living Lab: At-scale, real-world broadband testbed for connected rural communities
Iowa State is building a wireless “living lab” in central Iowa, laying the foundation for more affordable rural broadband service. The project will create a research testbed for a wide range of wireless technologies across Iowa State’s campus, the city of Ames and surrounding farms and rural communities in central Iowa – with an application … Continue reading Wireless Living Lab: At-scale, real-world broadband testbed for connected rural communities
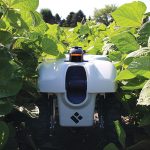
A.I. for Breakthrough Innovations
NSF AI Research Institute: Using digital twins to multiply crop production A new $20 million National AI Research Institute led by Iowa State will use the latest artificial intelligence tools to develop digital twins of individual crop plants and entire farm fields. The discoveries will help plant breeders improve crop varieties and farmers boost production. … Continue reading A.I. for Breakthrough Innovations
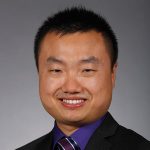
Tapping smart meters’ potential for grid resilience
Problem: Enhanced electric grid monitoring is needed to promote renewable integration while ensuring reliability, but current approaches rely on expensive sensors. Smart meters that electric utilities are already using for billing have potential, but without new computing innovations, smart meters only can provide limited insights into grid performance. Project: Wang will unlock the potential of … Continue reading Tapping smart meters’ potential for grid resilience
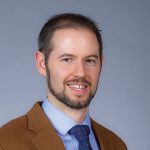
Biomanufacturing better treatments
Problem: Therapeutic cells show promise as a new treatment option for chronic illness, but advances must be made in manufacturing reproducibility to get therapeutic cells out of clinical trials and into widespread use. Project: Reuel will develop novel, real-time sensors and reinforcement learned (RL), dynamic control policies to improve reproducibility in large-scale manufacturing of differentiated, … Continue reading Biomanufacturing better treatments
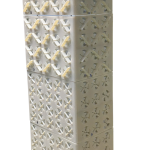
Smorphacade
“The Smorphacade project is the first-of-its-kind collaboration between structural engineers, wind engineers and control engineers to turn a passive building façade into a live façade that protects the building against wind load and turbulence,” said Alice Alipour, associate professor of civil, construction and environmental engineering. Alipour leads a team that’s combining a network of pressure, velocity and acceleration sensors strategically positioned on building surfaces. When excessive vibration-causing flow conditions are detected, the Smorphacade will change surface roughness or smoothness to mitigate inter-story building movements.
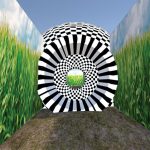
Virtual Reality, Real Cybersickness
Cybersickness. No, it’s not being tired of the constant stream of new emails in your inbox. It’s the physical illness some people feel in virtual reality environments. Angelica Jasper, a Ph.D. student in Humana Computer Interaction, is studying how to prevent VR users from experiencing nausea, disorientation, and oculomotor strain.
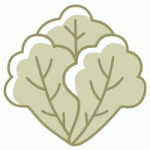
Engineering sustainable, safe food from the field to the table
A team led by Hongwei Zhang, professor of electrical and computer engineering, has developed CyNet, an open-source, wireless networking infrastructure to support data-driven research. CyNet takes on the challenge of quickly and reliably transmitting agricultural measurements from the crop field to plant scientists’ computers – and serves as a prototype for bringing much-needed broadband to rural areas. Food safety testing usually takes place in the lab by highly training technicians, but on-site, real-time, low-cost monitoring is our best tool to stop contaminated food from reaching consumers. Carmen Gomes, associate professor of mechanical engineering, is making key innovations in biosensor fabrication and system design to ensure food safety.
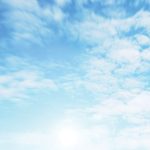
Boeing Undergraduate Research Fellowship program takes flight
A new partnership with Boeing pairs undergraduate students with College of Engineering faculty and Boeing engineers to get hands-on research experience in cutting-edge projects in aerospace engineering, cyber security, autonomous systems, machine learning and more. “The Boeing Undergraduate Research Fellowship has created opportunities for undergrads to learn research by doing, work on high-impact projects, and get familiar with the intellectual property considerations of industry-backed research,” said Arun Somani, associate dean for research, Anson Marston Distinguished Professor in Engineering, and Philip and Virginia Sproul Professor in Electrical and Computer Engineering.
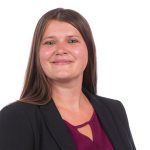
In this together: Collaborative networks create community resilience
Cyclone Engineer Cristina Poleacovschi studies how to build community resilience during challenges like natural disasters or economic shocks. Poleacovschi’s research suggests steps to increase shared resilience – even in unprecedented community challenges like the COVID-19 pandemic:
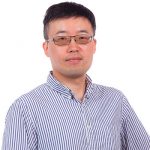
Storage systems keeping data safe
Storage systems are the fundamental computing building block of our modern lives – and like physical building blocks, computer storage systems must function well in fair weather as well as sudden disturbances to keep data safe.
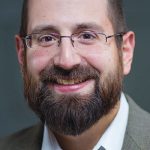
Ecosystems of support
Promoting an accessible, responsive approach to engineering education A new initiative in the Department of Electrical and Computer Engineering will help a pool of talented students pursue a degree in engineering. The project, called ECSEL: Electrical, Computer, and Software Engineers as Leaders, is part of the National Science Foundation’s Scholarships in Science, Technology, Engineering, and … Continue reading Ecosystems of support
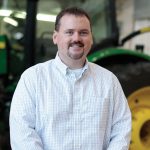
Market-ready solutions
Advanced ag machinery technology developed at ISU transfers to industry Matthew Darr’s research group strives to make an impact that extends knowledge and scientific development to the marketplace. “Seeing our results ported out to the public sector where we’re able to help agricultural producers with intelligent technologies — that’s our ‘why,’” he says. Darr, an … Continue reading Market-ready solutions