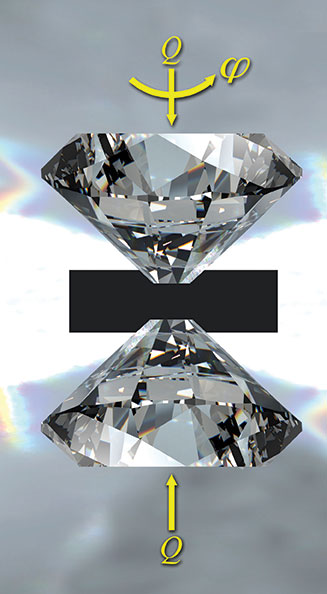
Search for new materials and phases under high pressure and large plastic shear
When you look at the properties and strength of a diamond, which is created under intense heating and pressure, it’s clear there’s value in understanding how it’s synthesized. Phase transformations under high pressure, like when graphite is formed into a diamond, are at the heart of the theoretical work Valery Levitas has been conducting throughout his extensive international career.
Levitas, Iowa State’s Schafer Professor and faculty member of aerospace engineering and of mechanical engineering, conducts fundamental research to predict and discover new phases of materials under high pressure. His work can be translated into engineering applications, including synthesizing superior materials for new technologies and products.
A significant part of his research investigates ways to retain high-pressure phases after pressure is released. To do this, he uses plastic shear, or an irreversible deformation that is applied with a rotational diamond anvil cell (DAC). He explains that plastic deformation not only changes the shape of a sample, it also changes the sample’s microstructure and generates new defects and phase transformations.
More importantly, the shear drastically decreases the pressure necessary to create desired phase transformations. “Near the defects we create, there are regions with concentrations of large stresses, which can be considered as pressures in different directions,” he says. “Instead of applying external high pressure, we apply a lower value of pressure coupled with large plastic shear to generate new defects.”
Using a rotational DAC in place of a traditional DAC has required Levitas to develop a new multiscale theory to explain the interactions between phase transformations and plastic flow under pressure. He says this is because unlike traditional high-pressure physics, which operates with the single parameter of pressure, he has to understand the effect of six components of stresses and six components of plastic strains, as well as the effect of evolving defects.
The corresponding analytical and computational approaches he developed to support his theory explain mechanisms of strain-induced phase transformations at the nanoscale as well as the complex behavior of a sample in rotational DAC.
His research group has been able to predict and confirm new phenomena through experiments. Notably, the team has proven the possibility to reduce transformation pressure by an order of magnitude to transform boron nitride from graphite-like to superhard, which may serve as a precursor of new technologies. Experiments have also revealed a new amorphous phase of silicon carbide that may shed a light on how armor ceramics are damaged under projectile penetration.
Levitas began his work in Kiev, Ukraine, and brought his high-pressure theories and technology to the U.S. in 1999. It took him eight years to obtain his first federal grant on this topic from the Defense Threat Reduction Agency, but now this work is supported by the Defense Advanced Research Projects Agency, National Science Foundation and Army Research Office.
“As the only team in the world working on this topic theoretically and the only one in the U.S. performing experiments with rotational DAC, I’m encouraged to see interest growing,” Levitas says. “Having an understanding of materials, including how they behave in natural and technological processes like earthquakes, friction and wear, surface treatment, military applications, and mechanochemical processes like ball milling, will lead to ways of controlling these processes and creating even greater materials.”